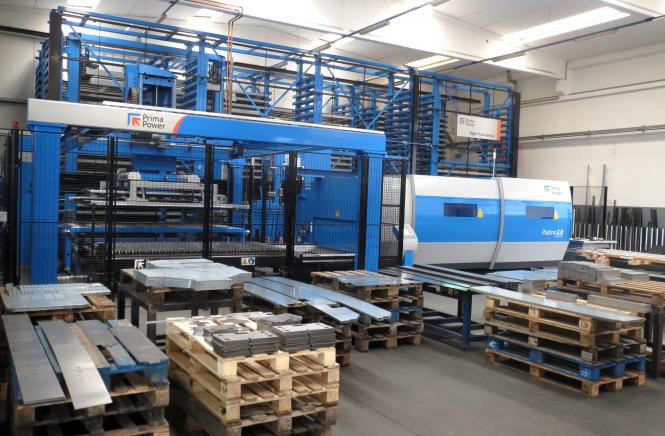
Automation as a Competitive Edge
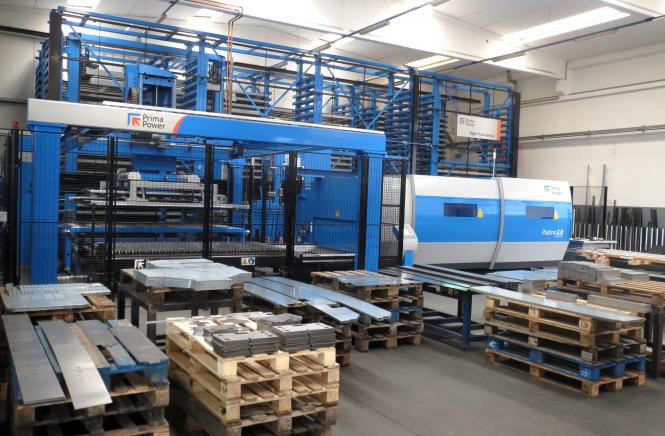
Thanks to integrating a Prima Power fully-automatic laser cutting system, consisting of a 6 kW Platino Fiber 2.0 laser cutting machine, along with a Night Train automated warehouse, Carpenteria Metallica Depedri has been able to increase productivity by 30%.
The activities carried out by a subcontractor are definitely complex, since they require the ability to combine production quality and the flexibility to switch into completely different batches in terms of size, materials, geometries, and speed to ensure timely deliveries to customers with increasingly tight time frames. These are critical issues that Carpenteria Metallica Depedri faces daily and can be successfully addressed due to its 60 years of business experience and supported by technologically-advanced sheet metal working machinery.
History of Growth
Carpenteria Metallica Depedri began operations in Villa Lagarina (Trento, Italy) in 1961 by mainly focusing on the construction of prefabricated metal structures and buildings of various types. In 1978, the company moved to its current location and started to expand the sheet metal working business. Never losing sight of its aim to meet customers’ needs as timely and efficiently as possible, the company made significant investments in equipment.
This focus on technological innovation became Depedri’s strength: new manufacturing processes were soon developed and launched by the company. This expansion resulted in enlarged facilities, a production boost, and a steady increase in turnover -- even during the recent economic downturn. Today, this company is a reference partner for a variety of applications in the sheet metal industry, including the assembly and finishing of heavy-duty structures. In addition to cutting, the company offers extremely accurate bending with its two 80 and 150 ton eccentric presses. It can perform a wide range of machining operations, including sheet metal stamping, even in the most demanding applications.
Ongoing Innovation
Depedri has gained great experience by increasingly establishing itself as a reliable, competent partner. While remaining a small company with less than 25 employees, its reliability and market focus have entitled it to gain the trust of large local companies operating both at national and, in particular, international levels in several diversified industries (lifts, shelving, furniture, doors, stoves, bathrooms, agriculture, and many others). Franco Depedri is the owner of the company founded by his father Aldo. Today, Franco’s children, Andrea and Laura, also work at the company.
"Thanks to this system, we can now manufacture workpieces at a 10 times faster speed than the previous machine."
Franco Depedri, Owner of Carpenteria Metallica Depedri
To be capable of acquiring orders in a competitive and fastpaced market, leveraging excellent technologies is a top priority, along with a need for the company to be organized in such a way as to effectively manage and fulfill orders. The Trentino-based company has renewed its equipment in the last few years, starting with an E6x punching machine with a Prima Power Compact Express. It is a system able to process single workpieces or series. Process control and accurate diagnostics ensure top-quality machining and scrap minimization, thus combining the highest productivity with an efficient management economy. The system has 60 tool stations, including threading tools, and variable height or continuous deformations. The machine is also equipped with a Compact Express automatic loading and unloading system.
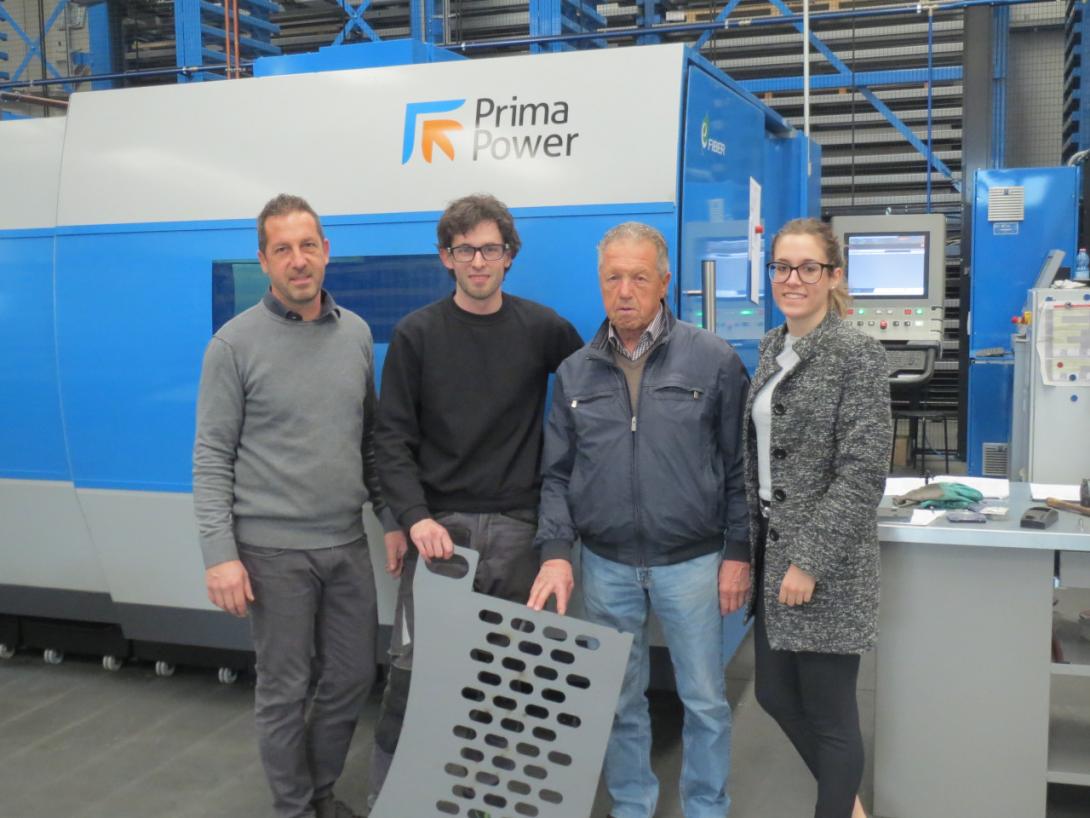
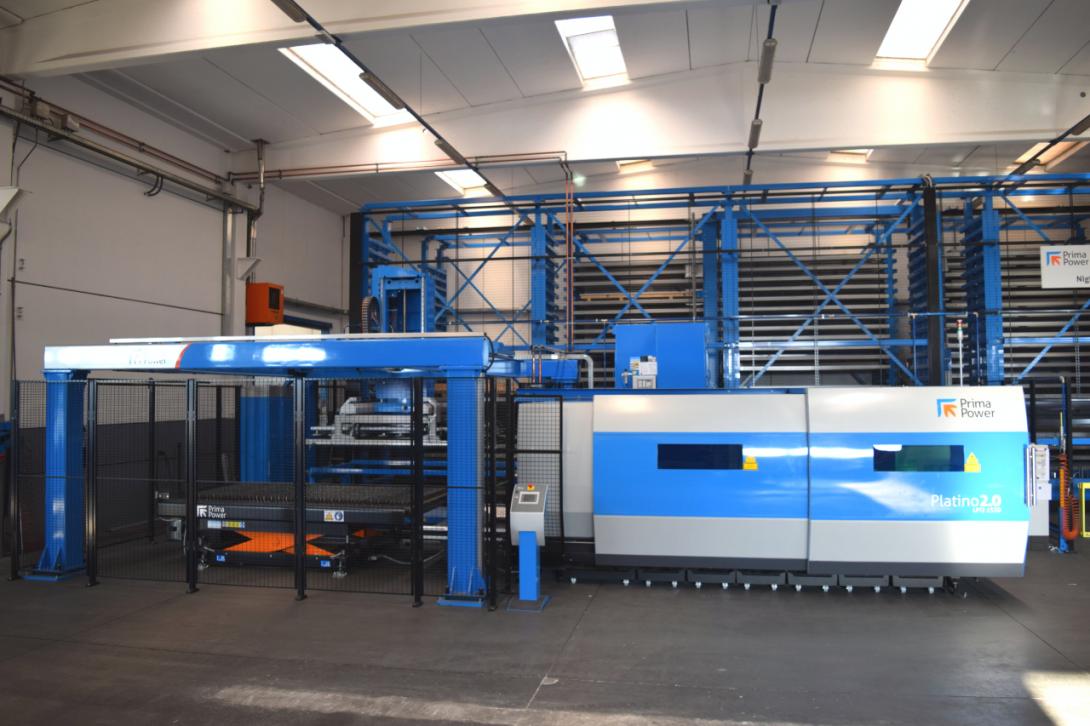
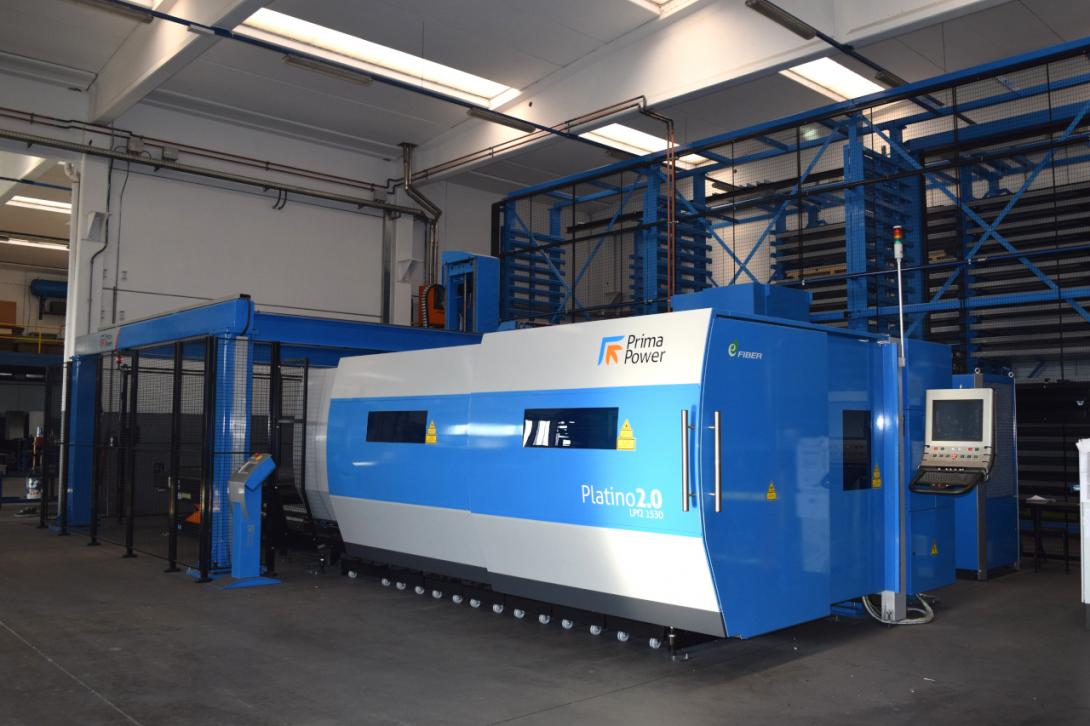
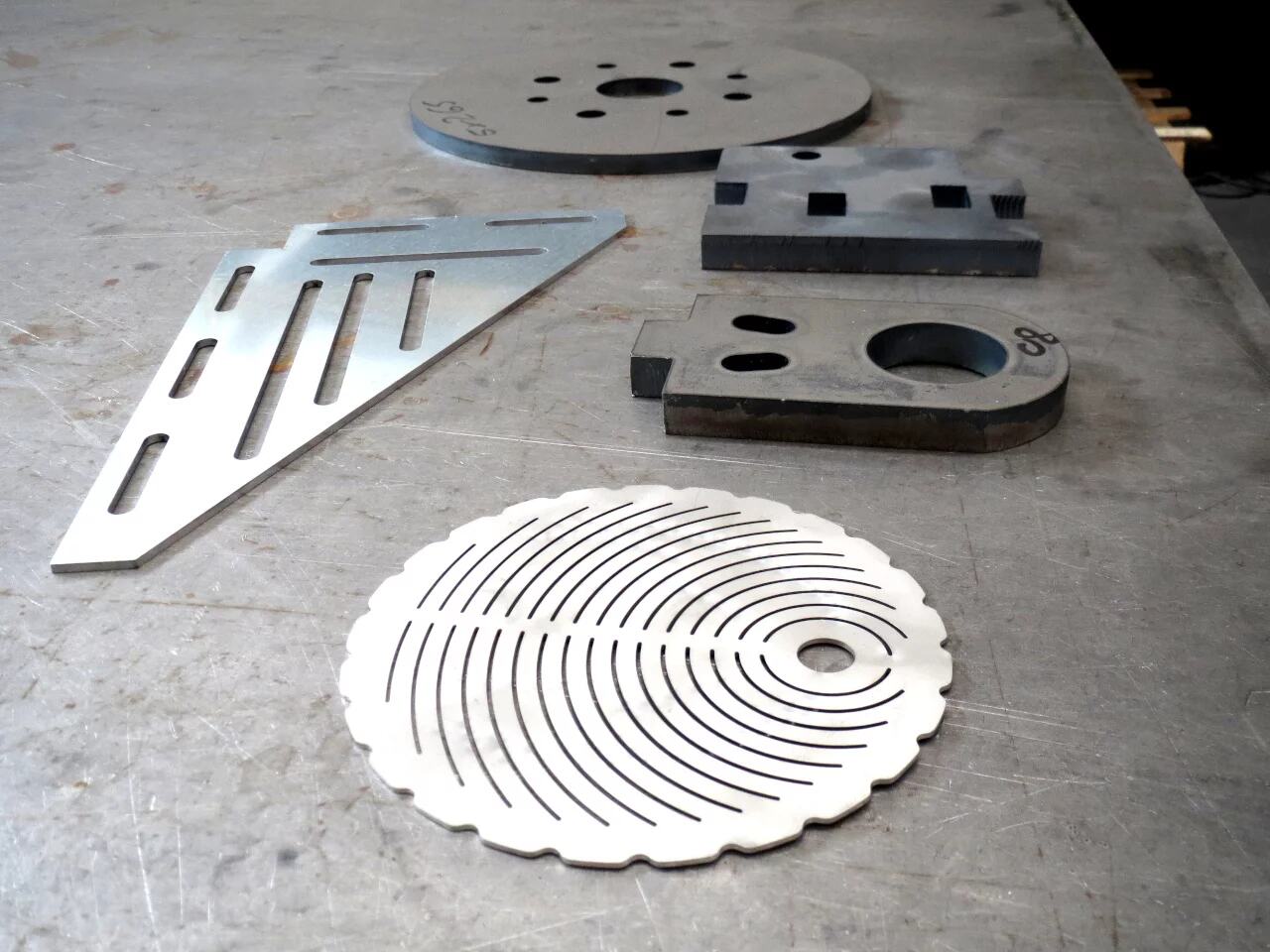
A Strong Relationship
The relationship between Depedri and Prima Power has continued to grow over the years. “Before making our choice, we had been carefully observing Prima Power’s machines, even during trade exhibitions, finding a good quality/price ratio and satisfaction from their users,” explains Depedri. “These aspects, combined with a number of major features, convinced us to select a Prima Power turret punch press five years ago, and to consolidate our relationship over time by later purchasing a laser cutting machine that has been operating successfully for nearly two years. As a result, we managed to enlarge our customer base, meeting all work requests, and boosting turnover by over 30%.”
Platino Fiber 2.0 laser machine’s productivity, is further enhanced by the combination with a Prima Power Night Train FMS warehouse, to manage the sheet metal to be loaded as well as handling the finished parts, which makes it an extremely efficient system. The introduction of this fully-automated laser cutting system makes it possible for Depedri to offer great cutting quality for steel, stainless steel, aluminum, copper and brass, with a wide range of automatic changeover nozzles suitable for any application.
The Platino Fiber by Prima Power can cut any steel and stainless steel profiles up to 20 mm and 15 mm thicknesses respectively. Cutting is done with no burrs on corners or edges, with a minimum heat supply on the workpiece. This is accomplished with a new fiber laser head and adaptive collimator, equipped with a single lens for cutting sheets of any material and thickness. The quality of the marking feature allows logo creation, inscriptions, and minute details.
"Thanks to this system we can now manufacture workpieces at a 10 times faster speed than the previous machine. This allows our machines to operate unattended even during night shifts. Prima Power is just what we needed to face the challenges in the field."
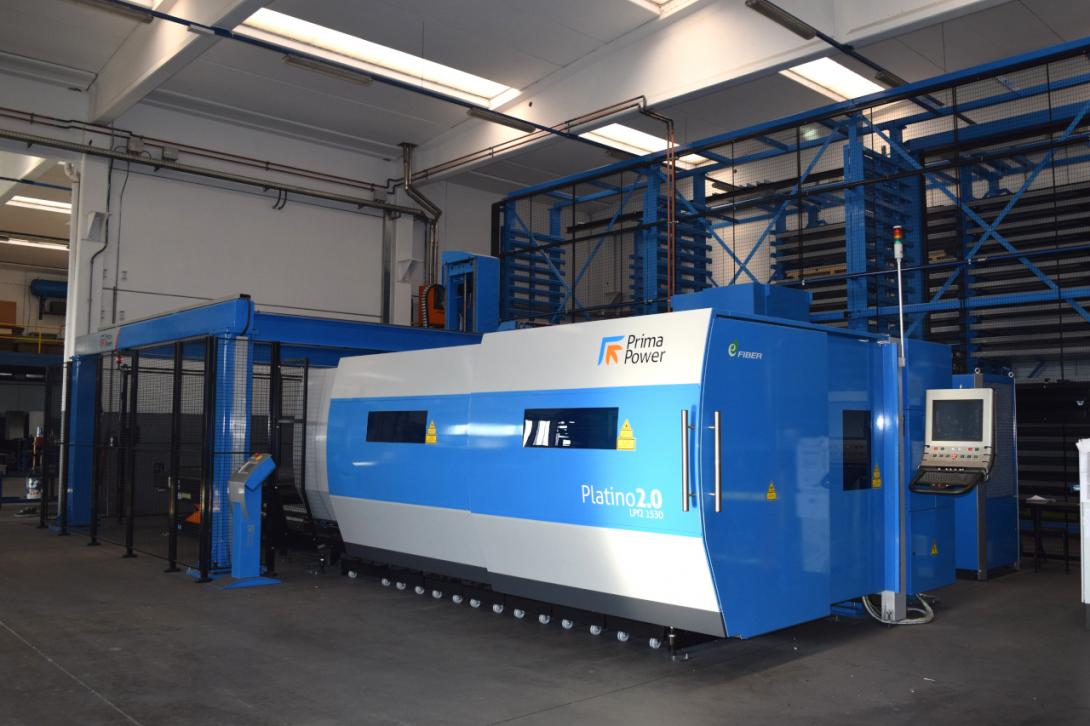

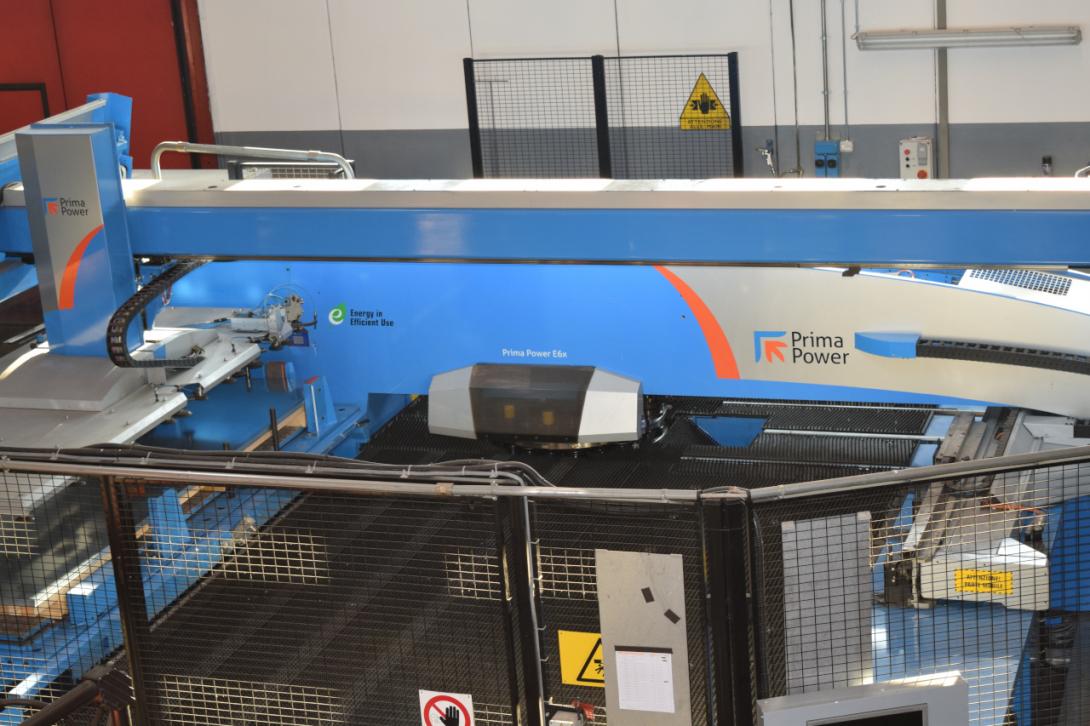
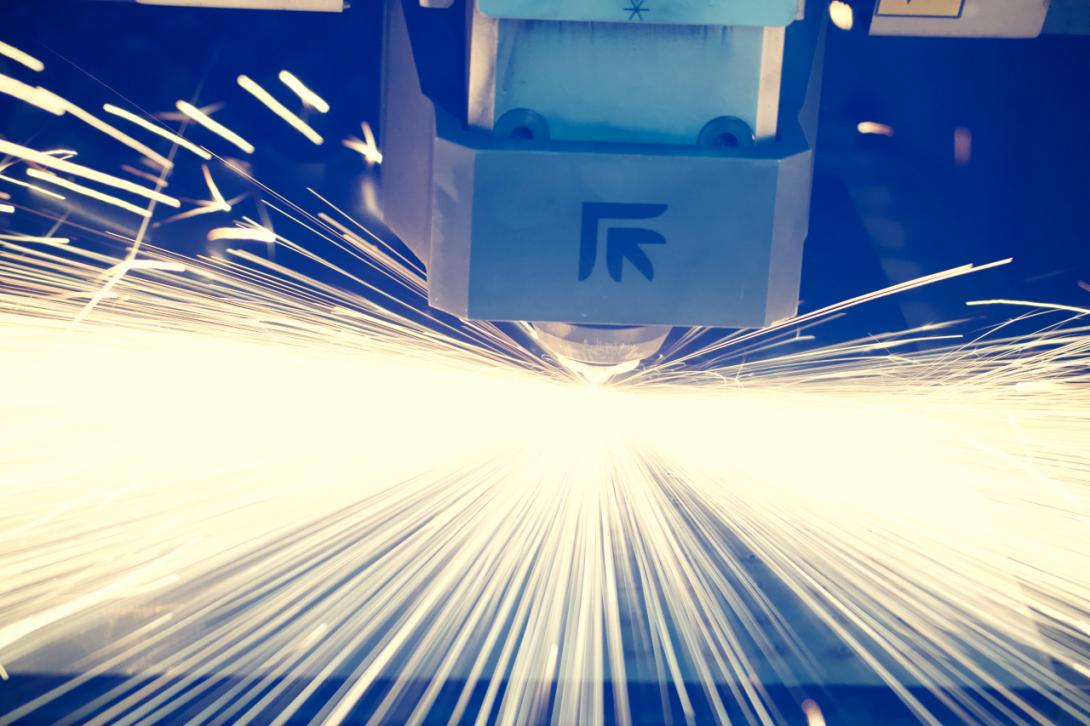
High Level Automation
The Prima Power Platino Fiber Laser is equipped with high power 6 kW laser source, a configuration unusual among subcontractors. It was a choice dictated by the opportunity to machine different volumes, and thus, immediately expand the customer base. The automatic sheet management system -- called Night Train FMS for its ability to operate night and day -- connects machines, programs, and processes in a single platform. Warehouse actions can be optimized based on other processes. The system supplied by Prima Power can ensure high-level automation.
“Thanks to this system - says Depedri - we can now manufacture workpieces at a 10 times faster speed than the previous machine. This allows our machines to operate unattended even during night shifts. There has been a dramatic change in manufacturing methods. Previously, we found it hard to find sheets or workpieces, as materials were stored in the workshop in bulk. Today, everything is accurately arranged, with operators really benefiting from this. Through a wide range of software-based data on the materials, we can decide strategic stocks well in advance, thus avoiding excessive or wrong purchases. Larger manufacturing volumes with less space requirement, shorter operating times in production changes, and for new products, virtually zero set-up times, rapid and automatic switching from one product to another... Prima Power is just what we needed to face the challenges in the field.”
"Thanks to this system we can now manufacture workpieces at a 10 times faster speed than the previous machine. This allows our machines to operate unattended even during night shifts. Prima Power is just what we needed to face the challenges in the field."
Are you looking for a similar solution for your company? Find it here
Night Train FMS®
FLEXIBLE MANUFACTURING SYSTEMS