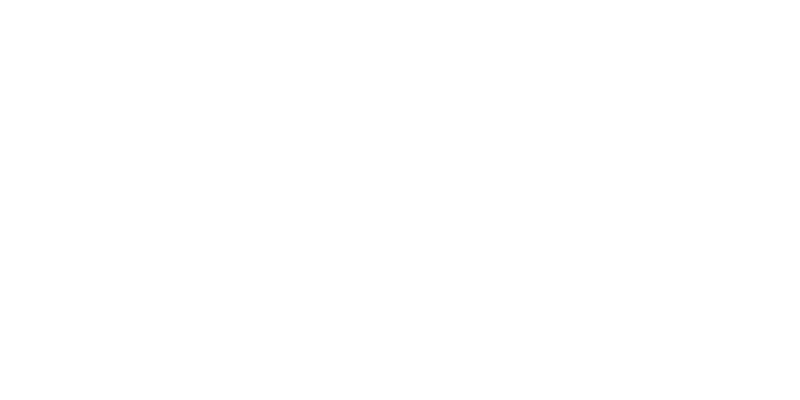
Snow- and ice-free roads even faster now
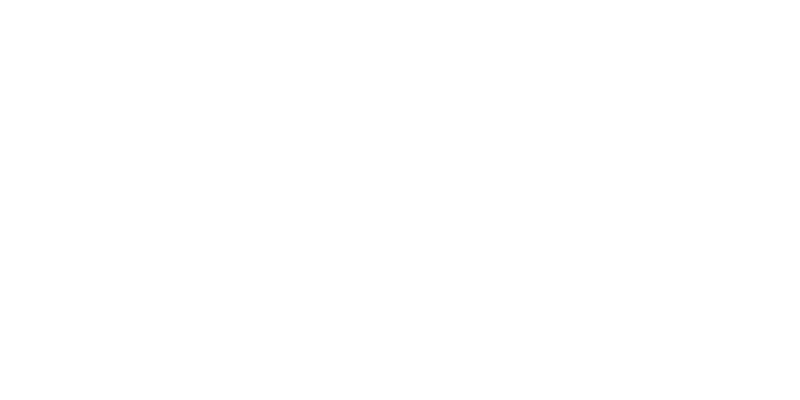
After about thirty years, Giletta, a company that is part of the Bucher Municipal group, a landmark in the production and sale of snow removal machines and equipment, decided to bring the steelwork department back in-house by installing a new fiber laser cutting system and a servo-electric press brake both by Prima Power.
A choice aimed at further cutting down on delivery times, to cater for a market that is not only seasonal, due to the intrinsic type of product, but also fluctuating and subject to many variables, not least the weather.
Science and technology are making great strides toward predicting weather conditions most accurately and reliably in a given geographical area in the future. Forecasts that, if not in the short term, are very often defined by the experts as “trends” and that not too rarely have surprises in store. So it happens that one has to face and manage unexpected emergencies due to heavy snowfalls that can bring whole cities to a standstill, or make roads, highways and airports conditions utterly complicated. The solution is relying on equipment and vehicles capable of effectively and promptly dealing with these inconveniences. It is precisely against this background that Giletta operates, a well-established international company that is currently part of Bucher Industries Swiss Group, specializing in the design, production and sale of snow removal equipment, such as snow plows and salt spreaders as well as street and airport sweepers. An activity carried out in Italy at its Revello (CN) manufacturing facility, located in the Po valley and framed by the Monviso landscape.
«Revello – Enzo Giletta, who owns the company with his brother Guido, explained – is the headquarters and main production site of Giletta SpA, where the Bucher Municipal Winter branch of Bucher Industries, which we have been a member of since 2002, is also located. This site, however, is complemented by the part of production that has taken place since 2013 at the Kaluga plant in Russia, intended for the local market, and that of the plants we manage by the German company Gmeiner, which became part of our Group in 2007.»
In the Cuneo area, Giletta can manage the entire development cycle in-house, from designing to manufacturing mechanical parts, sheet metal processing, welding, hydraulic systems, electromechanical systems, through to painting (with powder and liquid systems), assembly, testing and shipment.
«The electronic part – Giletta explained – has been actually acquired for a decade now by our subsidiary Saet, which was already involved in manufacturing some of the devices we needed, thereby meeting all our needs for this type of products.»
In the sheet metal processing department, there are two new high-performance systems supplied by Prima Power – Prima Industrie Group’s Machinery Division: a 6 kW Laser Genius 2040 with fiber technology, along with two storage Compact Towers with 10 + 15 pallets, and an eP 2040 electric press brake.
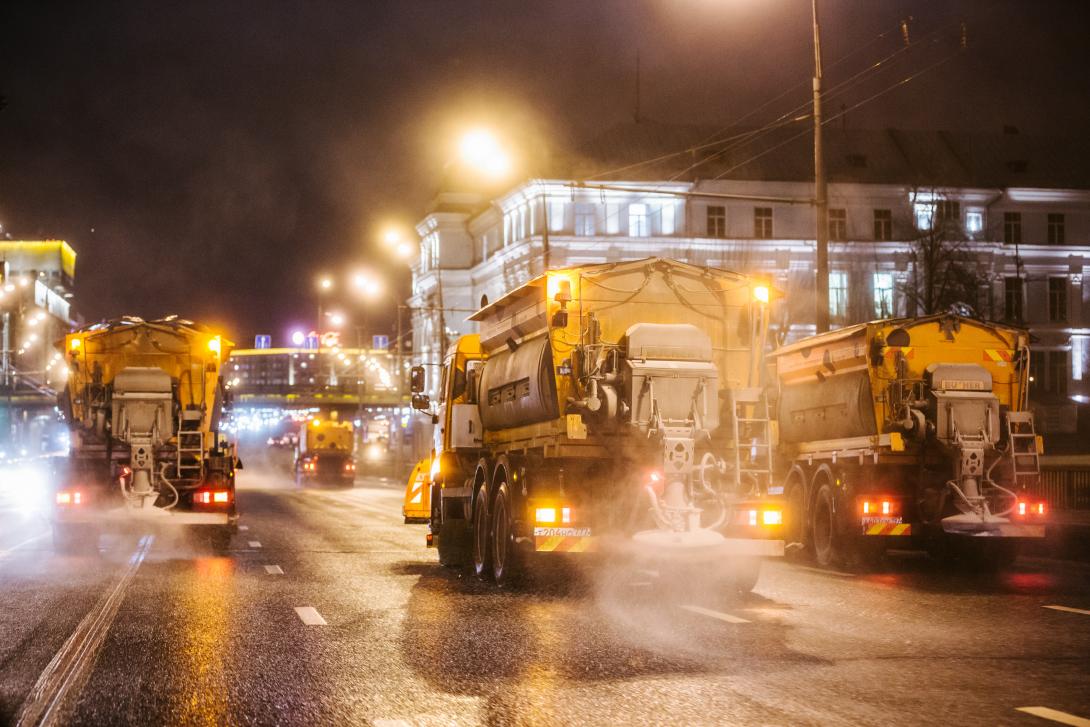
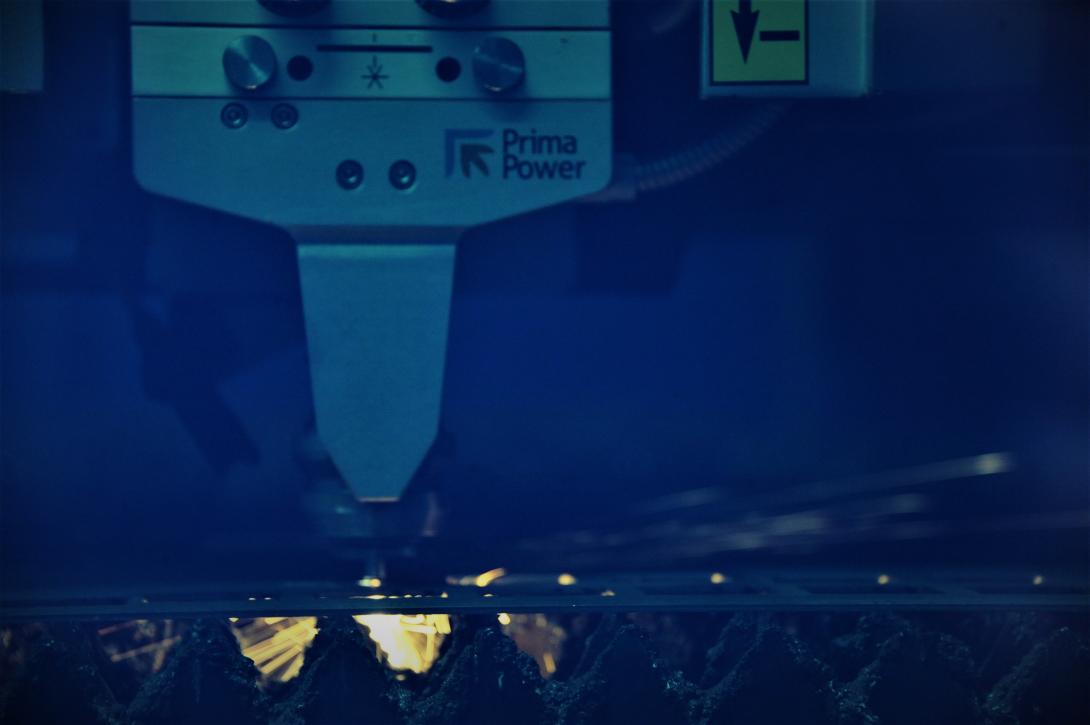
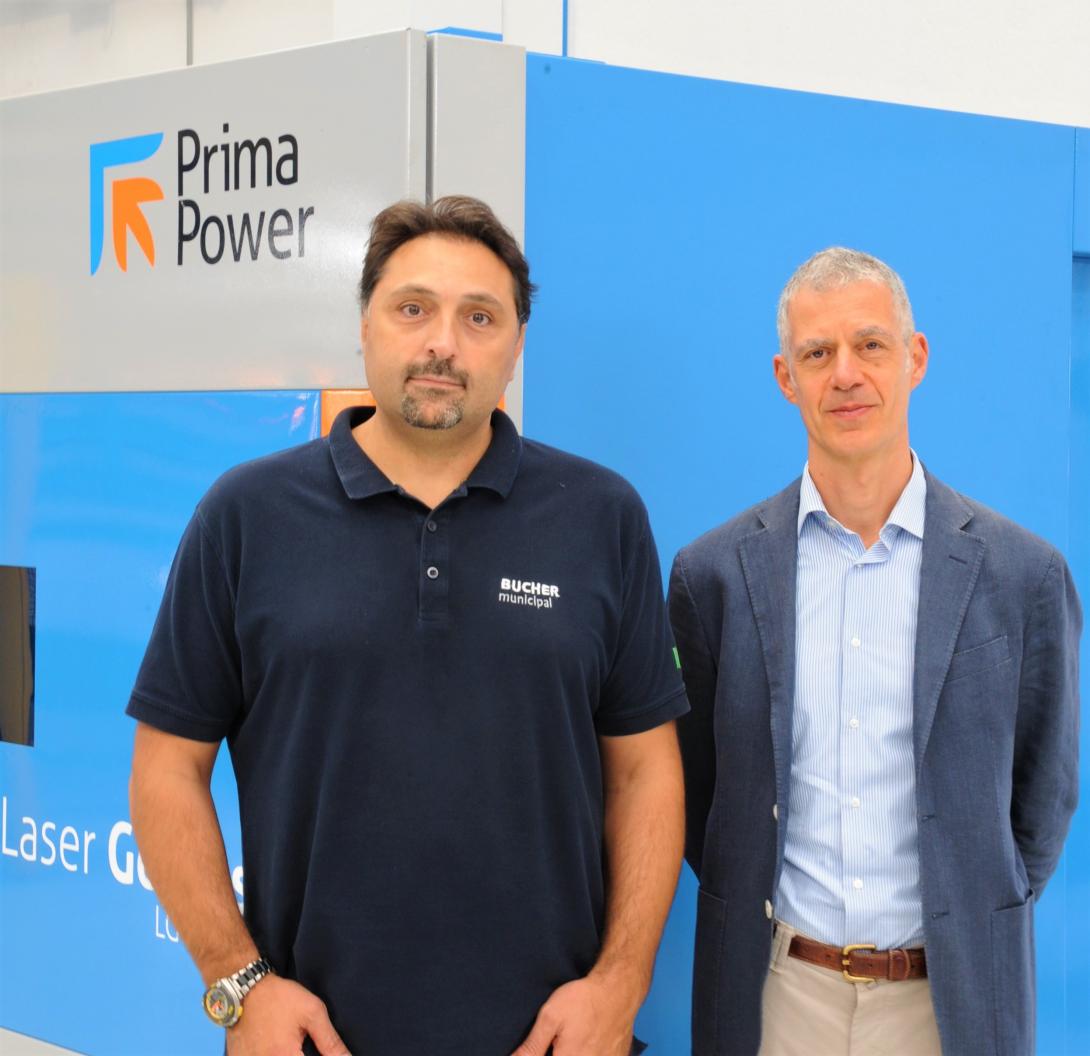
The turning point to increase competitiveness
The sheet metal processing department was (re)introduced into Giletta last spring, after being outsourced for about thirty years.
«The seasonal character of the market which we have always catered for – Enzo Giletta noted – urged us just before the 80s to reassess the resources available to us at that time, so as to redistribute them as best as possible and ensure more substantial growth for our facility.»
An operational choice that proved to be absolutely successful, thanks to a qualified group of reliable subcontractors. At least until the years after 2009, when subcontracting began to be reduced following the disposal of some activities or some supplier partners’ decreasing production capacity, precisely to face the difficulties of the period.
«Essentially – Giletta summarized – the delivery times of sheet metal products began to be extended, creating critical issues, and further weighing down the already great variability of the market in which we operate. Unfortunately, ours is not make-to-stock production. Or better, the components or part of them can be manufactured as make-to-stock, but not the final machinery or equipment. Our strength has always been flexibility and on-time delivery, but at a certain point these became too hard to manage with a view to sustainability and competitiveness.»
This is why, last year, thanks also to the National Industry 4.0 Plan, the company recreated the steelwork department in-house, choosing Prima Power systems to process steels (also stainless and high-strength ones) and wear-resistant sheets.
«We decided to turn to Prima Power –- Giletta confirms – for various reasons. First and foremost, the high level of quality and innovation of the technologies offered and, last but not least, geographical proximity, an essential factor to ensure sound support service in a very short time. We needed a solid, reliable partner, capable of supporting us very quickly in this production start-up. Also because in the new department, with only one system available, we can’t afford production downtimes at this stage, especially in view of the winter period which is peak work time for us.»
High productivity cutting and as much flexibility
A highly productive and precise fiber laser machine thanks to linear motors, innovative materials and smart process sensors, the Laser Genius 2040 chosen by Giletta for sheet metal cutting was developed by Prima Power to meet the most demanding requirements, and combines flexibility and dynamic performance with high levels of efficiency and accuracy. With a work area of 4,000 x 2,000 mm and a 6 kW source (also available with power ratings of 3, 4 and 10 kW), it ensures an even higher cutting quality thanks to the new head with adaptive optics for automatic management of the focal position and beam diameter and a quick, reactive and precise stand-off measurement. More generally, the system can be supplied with a series of option packages targeting diverse production needs: Smart Cut, for fast processing of thin sheets (max. 5 mm), allows cycle times to be reduced by up to 30%; Max Cut, for fast piercing of medium to high thickness sheets, makes it possible to reduce processing times by up to 40%; Night Cut, for intensive production, ensures greater safety in piercing and cutting processes.
«A system – Emiliano Francione, head of Giletta’s sheet metal working and steelwork department said – which we use to process up to 20 mm thick iron and up to 15 mm thick stainless steels with no trouble at all. Despite some early concerns, we can now cut even wear-resistant and high-strength steels without a hitch and with a very high quality.»
As already mentioned, the system is flanked by two Compact Towers intended for the automation of the raw and machined sheet metal flow.
«Storage towers with loading and unloading function for handling raw materials and machined sheets – Francione went on – ensuring a non-stop cycle. As a rule of thumb, the most numerous and standard batches are loaded on night shifts, leaving single pieces, urgent items and prototype pieces for the day shift when necessary, so as to make the flow as lean as possible. A significant advantage in terms of timing under the current market conditions, if compared to the previous management.»
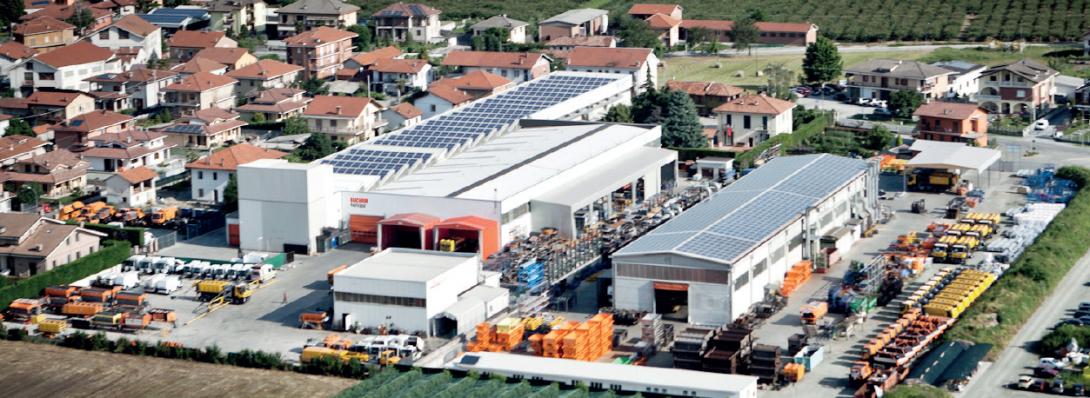
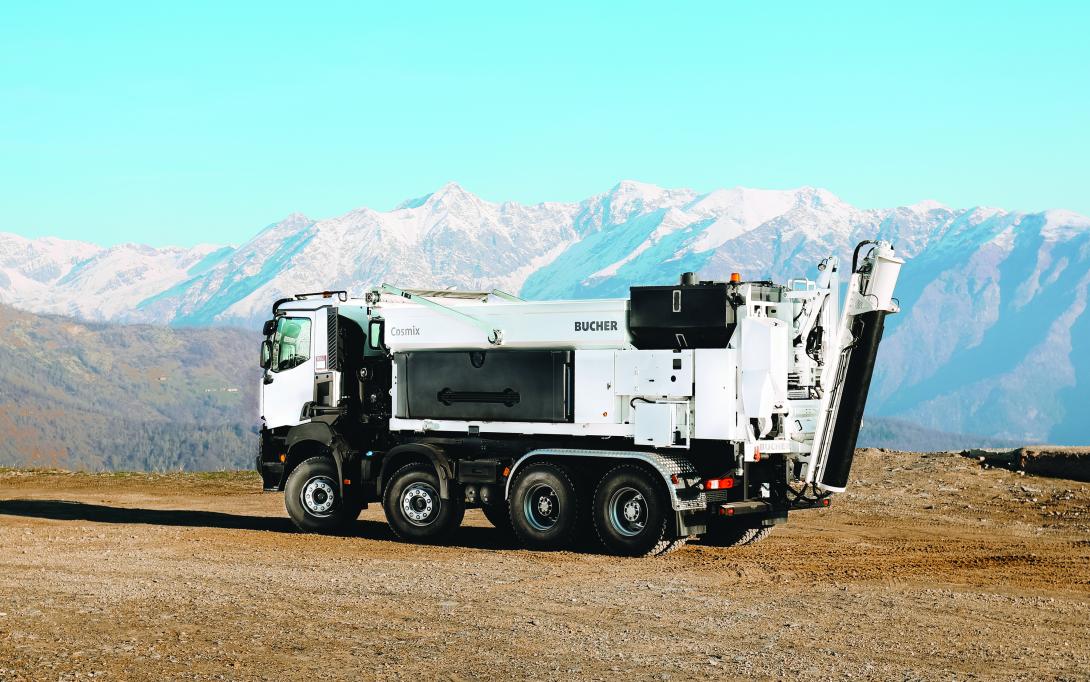
Fast, precise and efficient servo-electric bending
Available in 4 models with different tonnages and working lengths to meet any production request, the eP Prima Power press brake range combines productivity, precision, flexibility and reliability with a strong focus on the environment. Giletta identified eP2040 as the model that is best suited to their needs, with a useful 4,000 mm bending length and a tonnage of 200 ton. These are features which also combine the advantage of force transmission through a belt system with the uncompromising flexibility of CNC cambering compensation technology. The belt system, powered by sister company Prima Electro’s motors and servo drives, distributes the bending force over the entire maximum processable length. This technology offers greater control of movement and the utmost accuracy. With the CNC controlled automatic bending system, perfect results can be achieved in any bending condition, allowing for multiple bending combinations between the “V” jig and the required thicknesses. All this leads to significant advantages such as: no restrictions in the choice of the jig size in relation to the thickness of the material; freedom of bending in any working condition; perfect parallelism between upper and lower tables during processing.
«Accuracy and speed – Francione noted – that perfectly suit the thicknesses that we have to process every day, and that are performed at the highest quality level also thanks to our operator’s skills and the availability of Prima Power technology.»
The machine’s precision is also guaranteed by the sturdy, rigid “O” shaped structure that always ensures non-deformability of the structure, and therefore perfect perpendicularity between the upper tool and the sheet. This design also allows the side shoulders of the press structure to be positioned outside the work area, thus allowing for a back gauge covering all 4000 mm of bending length. Basically, with eP2040, a 4000x2000 mm sheet can be bent in the center, thereby creating a 4000mm long L, which is impossible with a standard hydraulic press brake. All this with repeatable positioning of the upper beam equal to ± 0.005 mm.
Very attentive to production efficiency, Giletta also networked the new Prima Power machines and related control software with its ERP management system, as required by Industry 4.0.
From snow to ice, through to construction cement
«Integrating a laser system and a press brake – Guido Giletta stated – is part of a growth strategy that, market conditions permitting, I believe can continue with new investments in the near future. From this point of view, given the swift evolution of technology, being able to rely on a partner like Prima Power, so capable of supporting us and helping us to be constantly abreast, is a real plus, a great added value to significantly optimize processes and production times.»
Production which today, for Giletta, means about 1,500 salt spreaders and 1,250 snow plows per year. Delivered to over 50 countries in the world.
«A make-to-order production – Giletta said – with a two-month average processing time from the order confirmation, which in order to be maintained and possibly further squeezed, must be monitored by careful management in a lean manufacturing perspective.»
The new technological process integration will be used by Giletta for a new project to be soon disclosed to the market, which this time will not involve snow or ice, but rather construction cement.
«For the developing countries – Giletta explained and concluded – that usually have a very hot climate, we designed and built the prototype of a vehicle equipped with a loading frame for the transport of raw materials, capable of making construction cement once on site. We strongly believe in this project as it goes beyond the traditional limits of liquid cement carrying concrete mixers, that over long journeys and in scorching climates risk bringing dry, no longer usable material to destination.»
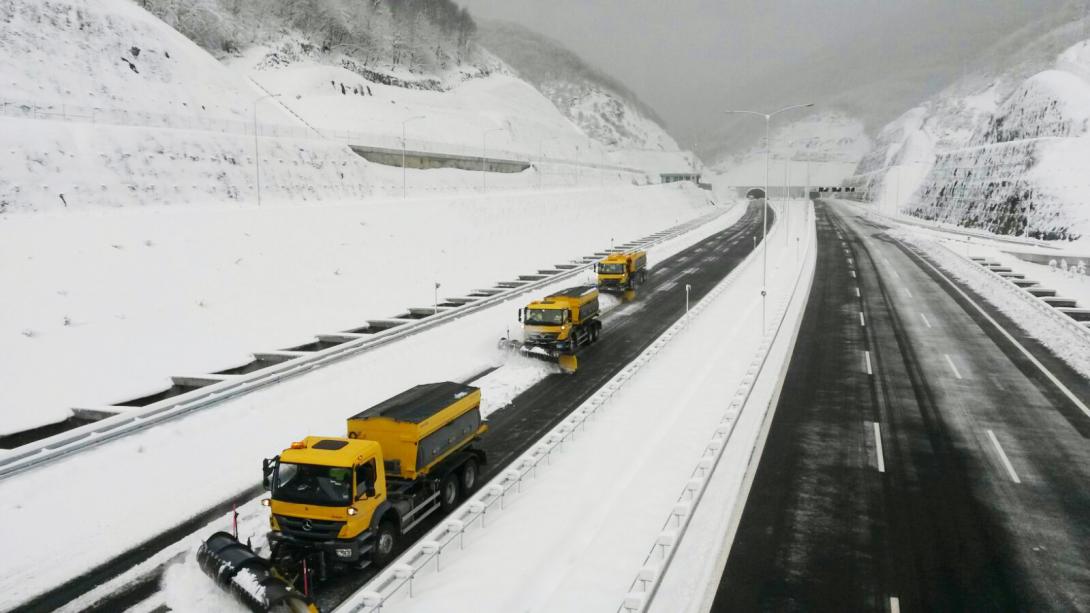
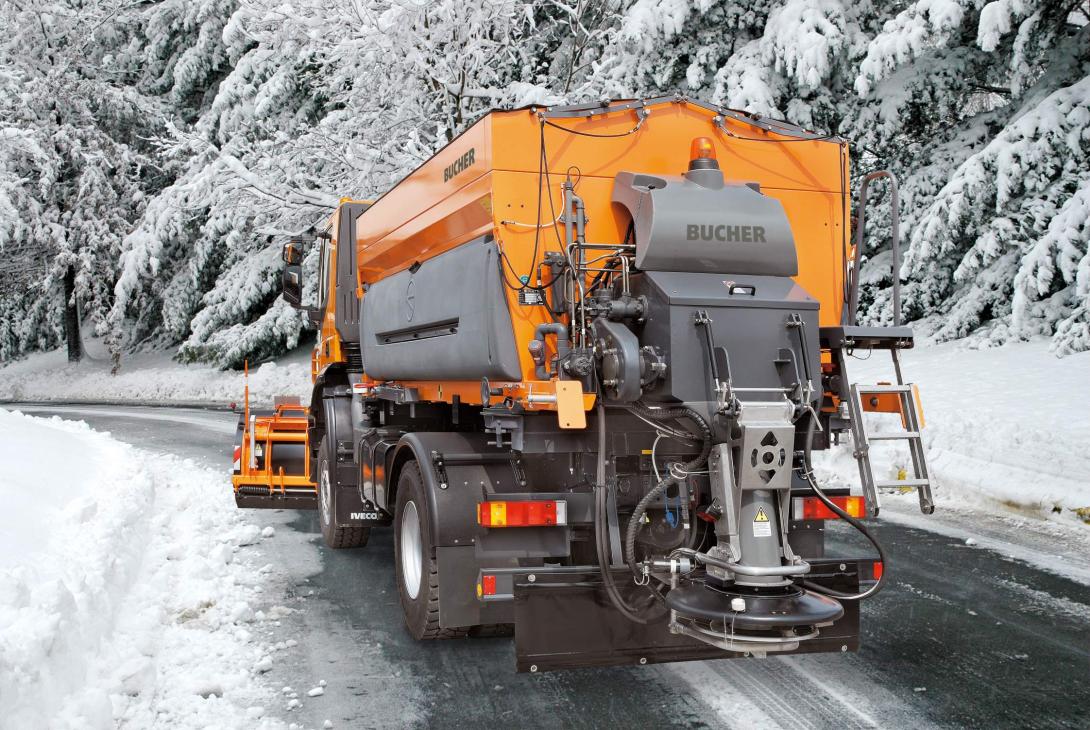
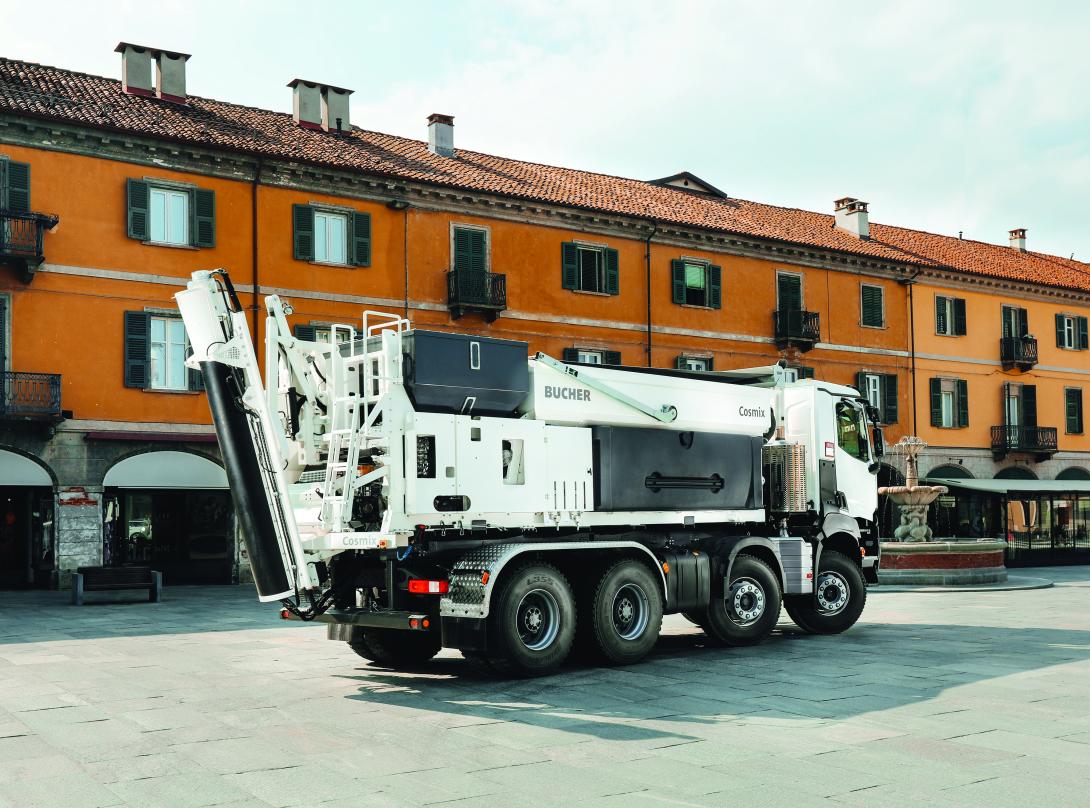
The company in a nutshell
Giletta Spa’s pathway is the result of ongoing evolution, which began in the mid-twentieth century when, in 1950, it was established first to market and then manufacture farming machines, a business that fifteen years later was turned into “cold” weather machines. In 1966 the company’s owner and founder was asked by the local traffic management authority to design and build a salt spreader.
«A machine – his son Guido, the current owner jointly with his brother Enzo, proudly recalled – that was made without being aware of what was available on the market in that field, but only leveraging the experience gained in the farming industry. This led to the construction of a much more reliable vehicle, with greater capacity than the competitors’ ones in those years.»
Features and positive feedback from the market that allowed the company to quickly specialize in the sector of winter service vehicles. Given the importance of the market beyond the Alps, in 1997 Giletta founded Arvel Industries, a French manufacturing unit, and became a landmark company in the industry in few years.
Another important step was taken in 2002, when the company joined the Swiss Bucher Industries group and, in particular, Bucher Municipal Division. This was a time of great change also in organizational terms, where a managerial approach took over and new markets were explored. Needless to say, technological innovation, that also led to filing various patents, has always played a major role at Giletta.
A complete series of all-electric salt spreaders was recently developed, capable of the same performance as traditional traction ones, but with a completely different environmental impact and efficiency level.
MACHINERY respectful of the environment
Giletta has been able to play an outstanding role in its field of expertise, standing out also thanks to all its technological innovation. Last but not least was the launch of some all-electric snow plow equipment on the market, about 4 years ago. Phoenix Electra, on the other hand, is the first all electrically-powered professional salt spreader. This new technology optimizes power, with 90% efficiency and 40% savings compared to a traditional spreader.
Prima Power has also been involved in the development of sustainable sheet metal working machines with high electrical efficiency for years. Adhering to the Green Means philosophy, Prima Power offers machinery that allows manufacturing with no waste and thus minimizing the environmental impact. The machines installed at Giletta are two clear examples of this. The high brilliance fiber laser the Laser Genius flat sheet cutting machine is equipped with ensures over 30% energy efficiency and low maintenance and consumption. The eP2040 servo-electric press brake allows for 50% energy savings compared to a similar hydraulic bending machine, and does not burden the company with additional costs to purchase new hydraulic oil and dispose of waste oil.
We use this system to process up to 20 mm thick iron and up to 15 mm thick stainless steels with no trouble at all. Now we can cut even wear-resistant and high-strength steels without a hitch and with a very high quality